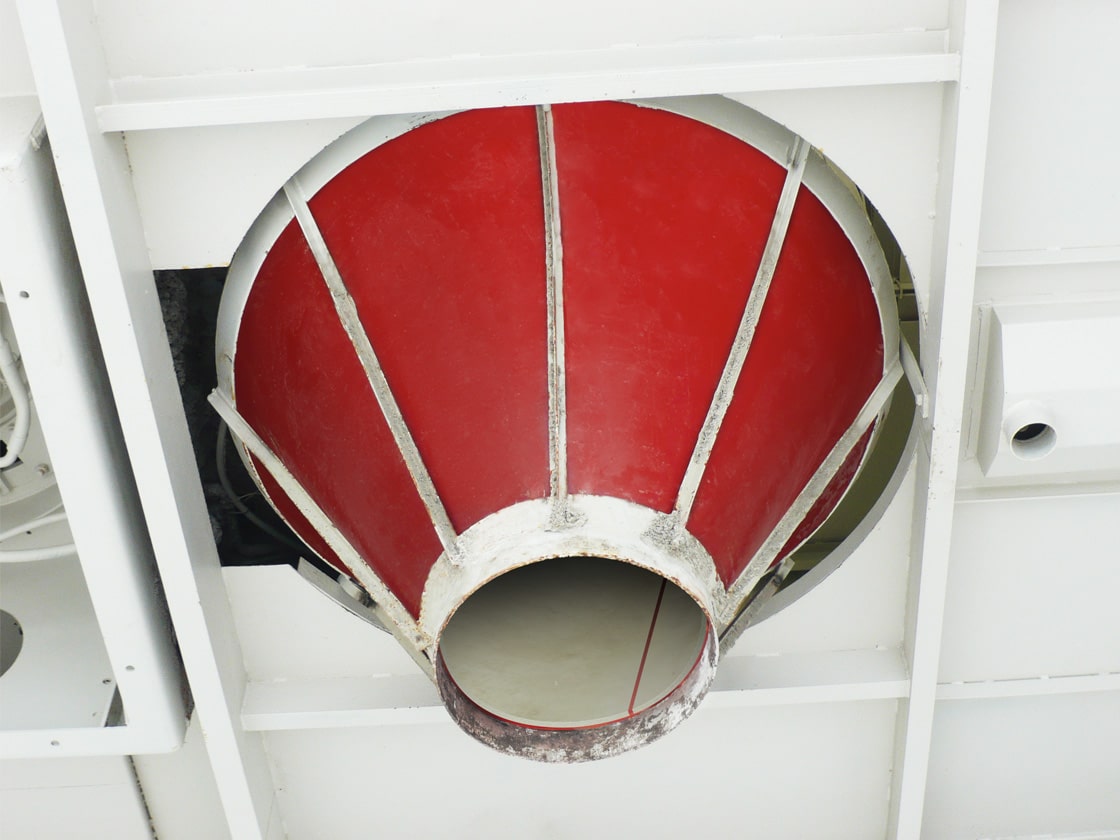
A leading national producer is making high volumes of what their operations manager describes as ‘the toughest concrete to handle that this company is currently producing’. The concrete contains both granite and steel fibres and is known for being extremely abrasive and aggressive towards the equipment.
The two mixers on site both had discharge cones lined with steel tiles. These discharge chutes would often block up completely, which would stop production and require the cones to be fully dug out by hand with vibrating tools. The regular cleaning routine also involved staff using vibrating tools for more than an hour per week and was causing overtime.
(Image: One of two identical discharge cones)
The steel tiles used to line the cones would wear quickly and require replacement after 6 months. Replacing them again required production to be stopped, as well as access equipment hired in and work to take place at height. The site was spending about £7,000 per year on replacing these tiles.
The operations manager replaced the steel tiles lining the two cones with ConeFlex, a low-friction and highly wear-resistant liner constructed from Hawiflex® polyurethane. The plant has had the ConeFlex liners in operation for 15 months, during which time the site has produced over 100,000m3 of highly abrasive concrete. The benefits have been highly significant in several critical areas.
Regarding health and safety, the use of vibrating tools to clean the cones has been eliminated, as well as the associated exposure to noise and dust. The ConeFlex liners have not required any changeovers or maintenance, so the working at height previously required by the steel liners has been eliminated.
In terms of whole-life cost, the ConeFlex liners cost around half as much to buy and install over the period. Buying and installing two sets of steel tiles cost around 40% more than ConeFlex liners did in the first year, but the ConeFlex liners have lasted into a second year of operation and are still going strong.
In terms of production and plant operation, the plant is now reportedly making 20% more concrete since the installation of the ConeFlex liners, with the daily cleaning requirement of the chutes down by 75% and blockages eliminated. The ConeFlex liners are cleaned daily with a Walter Washout hand lance. The site also reported that 8 full days of downtime has been prevented.
(Image: ConeFlex – simply washed down with water)
In terms of sustainability, at least one set of steel tiles has been saved so far, which saves the CO2 that would have otherwise been emitted to make those tiles. Diesel would have been burned to transport them, the access equipment, and the installation team to and from site.
• Highly abrasive concrete containing granite
• ConeFlex liners handled 50,000m3 each
• Blockages eliminated, 8 full days saved
• 50% cost reduction vs. steel tiles so far
• Cleaning time reduced by 75%