The problem
A busy plant being operated by a leading readymix producer was using an average moisture figure when weighing out raw materials for their production of a range readymix concretes.
The inaccuracy of this method combined with the natural variation of the moisture level within the raw material was causing an inconsistent amount of water to enter the mix.
This inconsistency led to the standard deviation of the concrete being 4.5, which is higher than it otherwise would be, as well as causing under-yielding and inaccurate raw material stocks.
The increased standard deviation, caused by the excess water, meant that ‘over-cementing’ was taking place in order to guarantee that the concrete would be of a suitable strength.
A report produced by the customer showed that the level of over-cementing was significant. The financial cost and CO2 emissions from the additional cement used were considerable.
How ConSpare found a solution
ConSpare has been supplying Hydronix moisture measurement equipment to the industry for decades. Its superiority over the ‘averaging’ method of measuring moisture is widely accepted.
Hydronix probes measure the moisture content of the sand accurately on a batch-by-batch basis, allowing the plant control system to automatically adjust the water input to compensate.
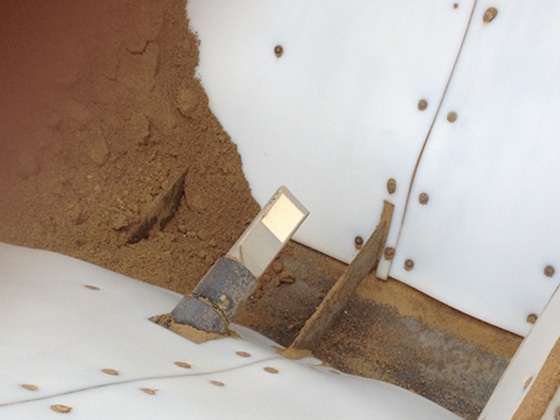
(Image: Hydronix probes were installed in the sand bins)
A report produced by the client stated that an average reduction of 26kg of cement was achieved per cubic metre of concrete produced. This is equivalent to 1413 tonnes of cement per year.
The scale of the cement reduction combined with other savings meant that in this case the Hydronix equipment was found to have paid for itself within 3 weeks of operation.
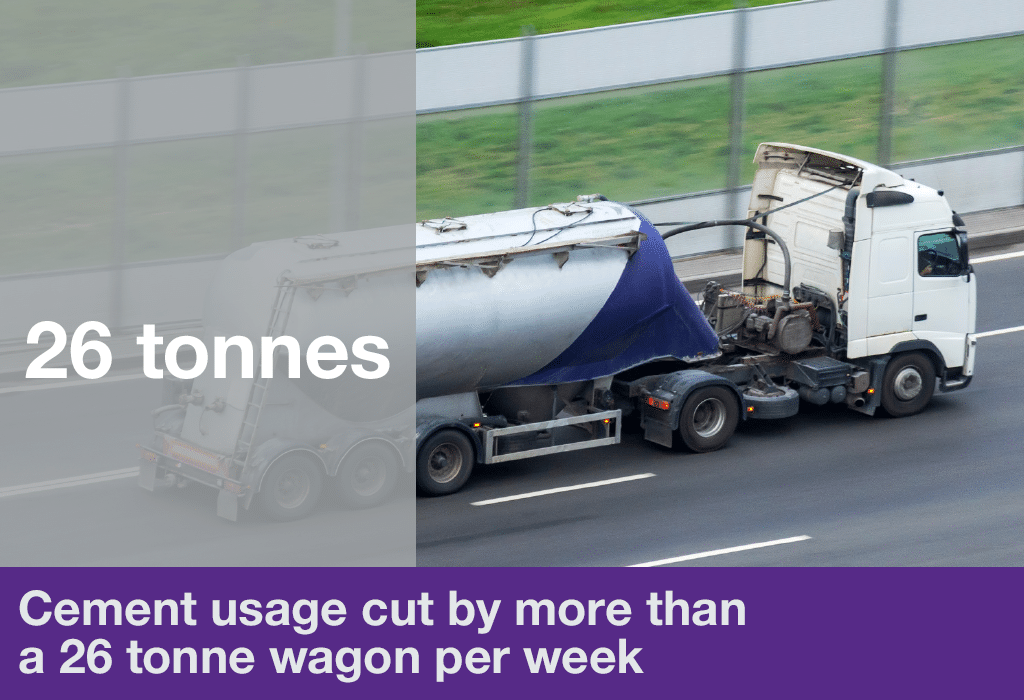
This is equivalent to an annual return on investment of over 2,460%. This was comprised mostly of reduced cement costs but money was also saved on sand and by having a lower SD of 3.5.
Additionally, assuming that 729kg of CO2 was emitted for every tonne of cement produced, this annual saving of 1413t of cement would reduce CO2 emissions over this year by 1030 tonnes.
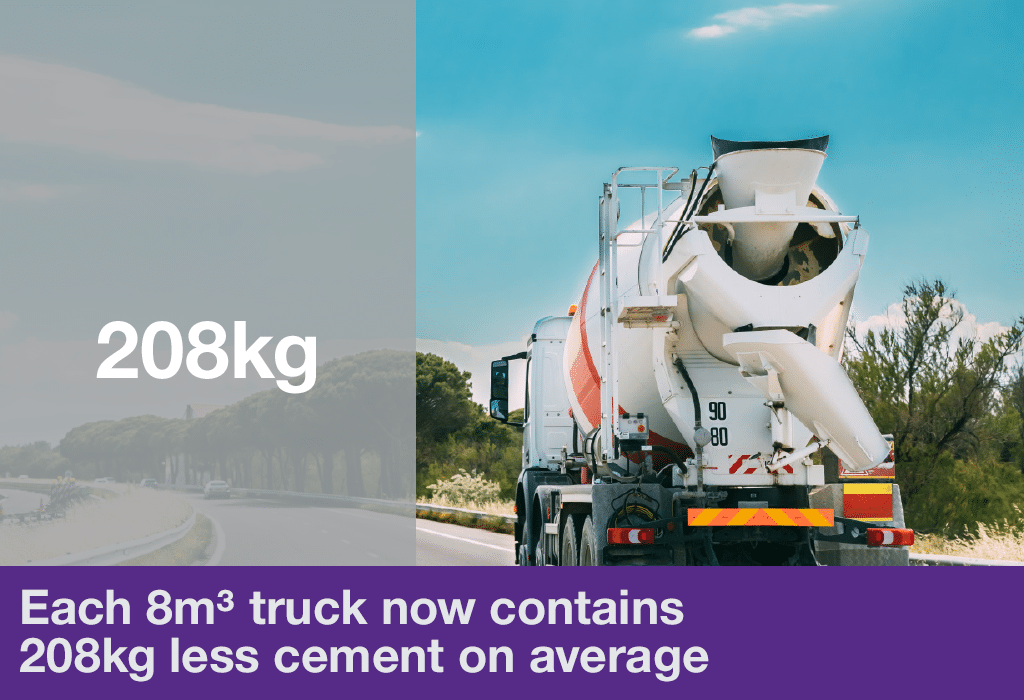
At cement prices of £130 per tonne, the cement saving alone would be approximately £185,000 per year. The use of cement replacements would reduce the CO2 but not the financial savings.
In addition to the many improvements reported by the team on site, the plant also received positive feedback from QSRMC.
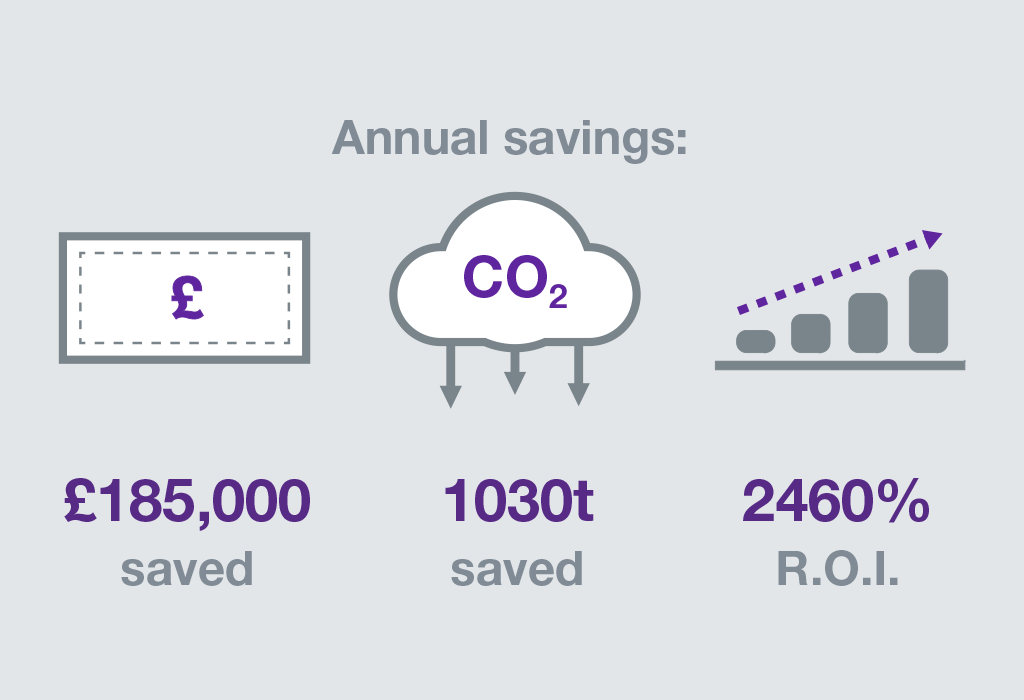