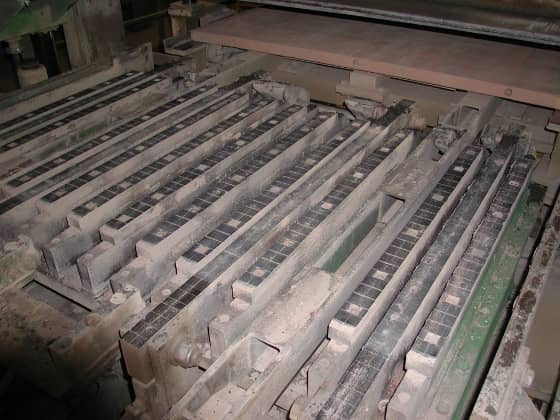
The performance of a concrete block machine has a direct influence on both the productivity of the plant and the quality of the concrete products. To keep it operating effectively a block machine requires maintenance, which causes downtime, and a common hotspot for maintenance is the vibration table liners.
This was the case at a leading national producer of concrete blocks. Due to the level of abrasion and the use of steel production boards, the OEM’s steel vibration table liners were wearing unevenly and relatively quickly. A shutdown was then required for the vibration table to be maintained, with the liners replaced entirely and the table reset every 6-8 weeks.
(Image: Block machine vibration table at client’s factory)
Adjusting and resetting the vibration table was a highly skilled yet laborious task that took the engineering supervisor the majority of a 6 hour shutdown to complete. The task was undertaken 6 times per year, resulting in around 30 hours of plant downtime per year. There was also the significant financial cost of purchasing 6 sets of new vibration table liners every year.
The activity was also extremely challenging for the team. The long hours and labour intensive nature of the task was wearing site staff down and detracting from other maintenance activities.
The maintenance supervisor contacted ConSpare to find a solution to the wear problems and ConSpareUltra PLUS vibration table liners were chosen to replace the OEM steel vibration table liners due to the use of steel production boards.
Steel boards present a challenging application to vibration table liners and ConSpareUltra PLUS uses specialist tungsten carbide facing segments which combine extreme abrasion resistance, a low co-efficient of friction and higher impact resistance.(Image: Special tungsten carbide segments developed for application)
The difference in performance has been staggering, with the first set of ConSpareUltra PLUS lasting 4 years before replacement, compared to the OEM steel vibration table liners lasting just 6-8 weeks. This means the Ultra PLUS set lasted almost 30 times longer, with 29 fewer changeovers, 29 times less installation downtime and 29 fewer sets of liners purchased over four years.
This impact on the performance of the site has also been transformational. Because ConSpareUltra PLUS liners wear so slowly the consistency and therefore the quality of the concrete products could also improve. The client states that the site now achieves improved strength, height and density of the blocks.(Image: ConSpareUltra PLUS providing 4 years service-life)
As the ConSpare Ultra PLUS liners only required fine adjustment rather than full replacement the need for maintenance shutdowns for the block machine was reduced. The client changed the frequency of their shutdowns from every 2 months to every 3 months, saving ~£36,000 per year in downtime costs alone.
Staff reported an improvement in safety and wellbeing due to the reduction of this physical and demanding task. Scarce maintenance time has now been reallocated elsewhere and production volumes have increased to over 2.5m blocks per year
• Service life of liners increased by a factor of approx. 30
• Block machine downtime reduced due to service life
• Production volumes increased due to reduced shutdowns
• Product quality improved due to consistency gains