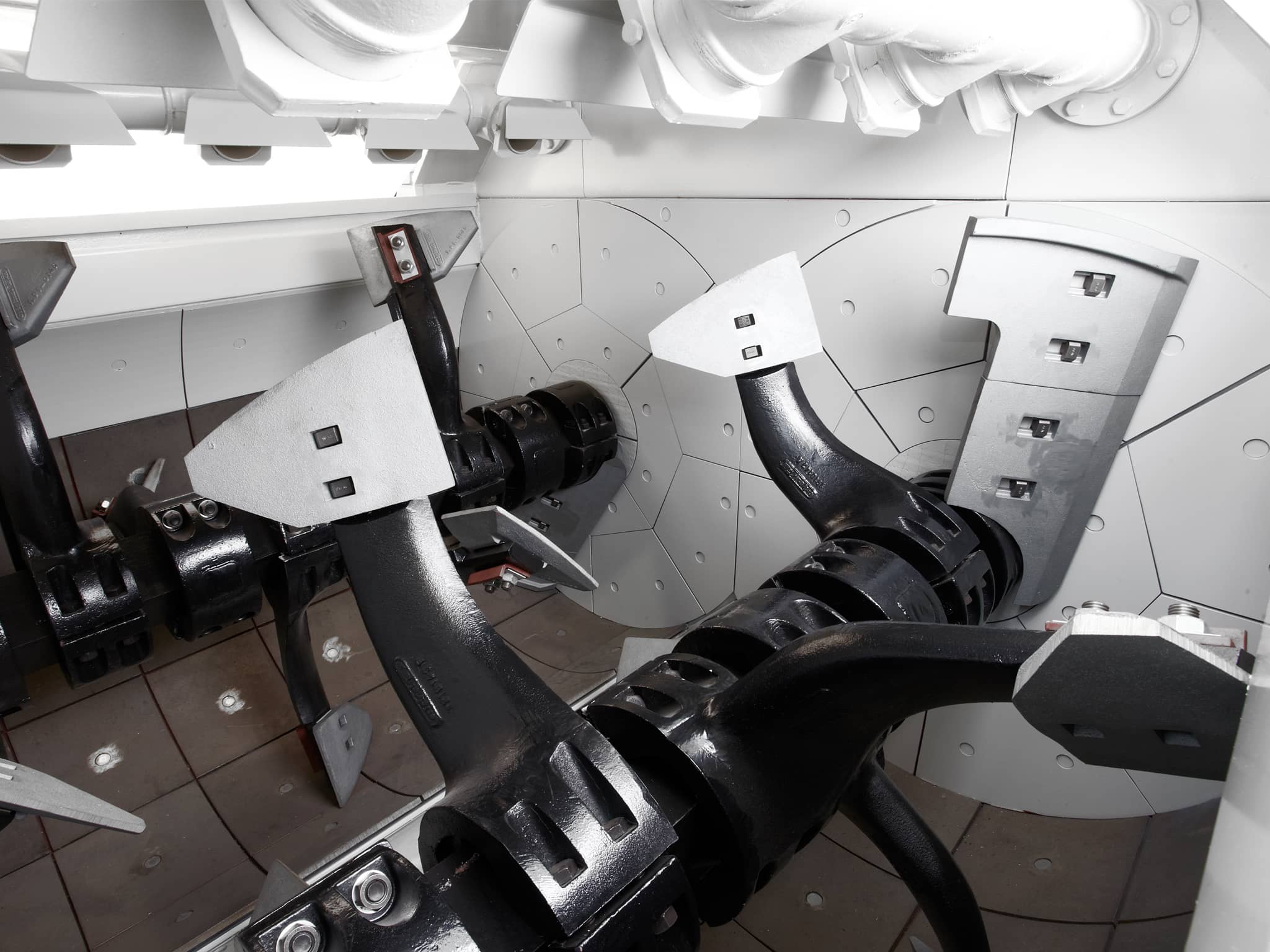
A popular make of twinshaft mixer being used by a major national concrete producer was using traditional cast steel mixing blades to produce concrete for the HS2 project. The site needs to produce an extremely high volume of concrete and so must operate effectively with very little downtime. The site often works long hours to complete each days production.
To keep production running smoothly the site had to spend a lot of time keeping the mixer clean. In addition to operating an OEM washout system, they also had to manually wash down the inside surfaces for 45 minutes per day and do a weekly deep clean where operators would get inside the mixer for 4-5 hours and use a breaker to remove the solidified concrete.
(Image: The 110V electric breaker previously used 4-5 hours a week)
This routine, while necessary, was far from ideal. Not only was this costing the site time and resource, but reducing the availability of the mixer as well. It was also causing staff to enter a medium risk confined space, use vibrating tools and be exposed to the attendant noise and dust. This kept site staff from being able to progress with other maintenance tasks.
The operations manager decided to try Hawiflex® mixing blades and the difference has been astonishing. Hawiflex® is a premium polyurethane material with great elastic and non-stick properties. This means Hawiflex® naturally resists build-up and, being slightly flexible, is also easier to clean. In this mixer concrete was sticking to the cast blades but isn’t sticking to the Hawiflex®.
In addition, Hawiflex® is elastic enough that the blades could be set closer to the outer wall without the worry of aggregate getting trapped and then cracking the blades or the wall tiles, as was the concern with the cast blades. The more closely-set blades provide a far better scraping action against the wall surface. As a result, the mixer effectively keeps itself much cleaner.
(Image: Hawiflex® premium polyurethane mixing blades)
The time spent manually washing out this mixer has dropped from 45 minutes per day with the cast blades to just 15 minutes per day with Hawiflex®. The time saved on hosing the mixer down is therefore around 10 hours per month in total, or 66% of the original time requirement. This also saves a lot of water.
The regular deep cleaning, which involves getting inside the mixer with a 110V breaker, has dropped from 4-5 hours every week to just 1 hour per fortnight. This is saving the site around 18 hours per month or 90% of the previous time requirement for this type of cleaning. This allows the plant to be much more productive.
This means that the blades are making a big difference to working conditions on site, with big reductions in routine exposure to vibration, dust, noise and confined spaces. The site is therefore saving around 28 hours per month on mixer cleaning in total, as well as the time required to isolate the plant and complete RAMS.
“It is still too early to say which last longer, but even if the Hawiflex® blades don’t last as long as cast ones it doesn’t matter, the savings on cleaning time, downtime and overtime are so huge that they outweigh all other considerations. ” – Operations Manager HS2
• Daily cleaning with water lance down by 66%
• Deep cleaning with 110V breaker down by 90%
• Reduced exposure to vibration, noise & dust
• Reduced entry into a confined space
• Overtime costs down significantly