Mixers
TEKA pan, planetary, turbine & twinshaft mixers. High efficiency, low maintenance mixing.
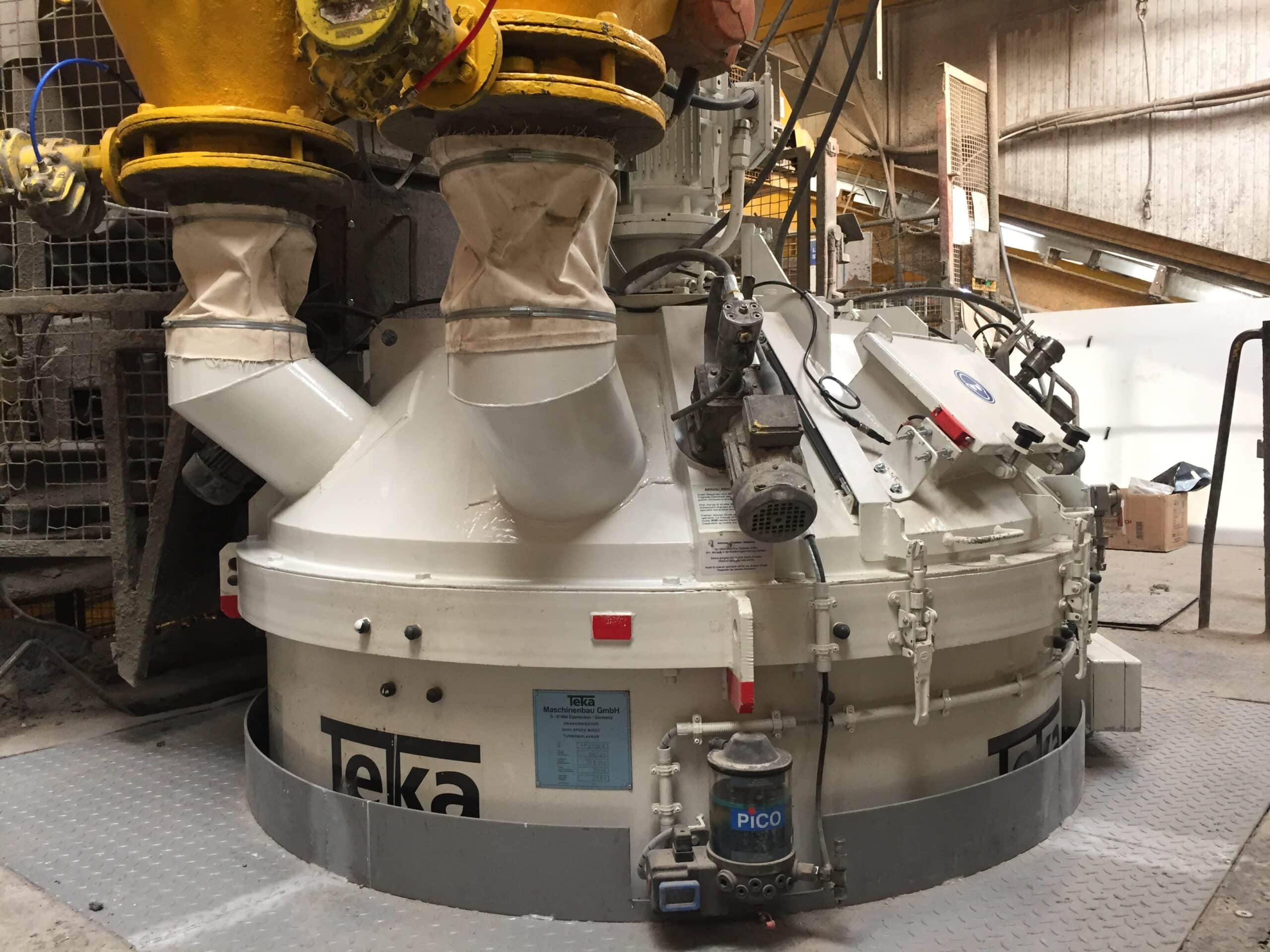
New technology constantly makes big promises – better performance, higher quality, lower costs. But when installed, it does not always live up to the hype, especially when it comes to a finely balanced process such as block making. But it is not always the technology that is at fault here.
Often, the problem lies in the fact that concrete production is viewed as separate manufacturing elements, as opposed to a series of interrelated processes. It is important to realize that, when it comes to the production line, the end product is only ever going to be as good as the weakest link.
If businesses are to reap the rewards of investing in new concrete technology, then moving from being product-led to process-led and looking at the manufacturing process as a whole can be hugely beneficial. Businesses need to make sure that when they get that new bit of kit, they build in the necessary changes upstream and downstream in the process to allow it to perform at its absolute best.
This is exactly what Besblock, the longstanding, family-run block-making firm did at both of their factories in Telford. Teaming up with concrete production specialists ConSpare, they have transformed their plants with a series of plant upgrades centred around the introduction of two TEKA planetary mixers, a 1m3 TPZ1500K and a 2m3 TPZ3000F, both of which provide the next-generation mixing technology the company was looking for.
(Image: The TEKA units have provided the next-generation mixing technology Besblock were looking for)
Besblock are now able to mix round the clock, with one mixer running 24h a day, five days a week, with no downtime, while also exponentially improving the quality of the blocks. But while the mixers are undeniably at the heart of the plant, they do not operate in isolation and it took a review of the entire plant’s performance to help make these improvements possible.
When the first blocks came out, the difference was unbelievable – you could instantly see it. We were totally blown away by the improvement in quality. The fact that we have been able to ramp up our production to meet our growth plans without compromising on quality has made this investment worth every penny,’ recalled Besblock director Nigel Chadwick.
The block-making firm brought in ConSpare because of their close relationship with the TEKA brand, but it was their creative thinking and ability to make the process perform better as a whole that ended up having the greatest impact.
‘Businesses today see investing in new technology as a silver bullet. But to get the best out of the technology, taking a holistic view of their processes is vital otherwise they will end up throwing good money after bad. It’s about making it better at every stage of the process to unlock the technology’s – and the plant’s – optimum performance’, explained Steve Peterson, engineering director at ConSpare.
(Image: One of Besblock’s new TEKA planetary mixers, supplied and installed by ConSpare)
As part of the plant assessment, ConSpare employed their Make it Better approach. By taking a closer look at a plant’s overall performance at all five key stages of the production process – storage, conveying, batching, mixing and discharging – businesses can quickly identify any potential bottlenecks that may hamper the performance of the new technology. This approach will not only help iron out all potential problem areas, it will also give plants greater visibility, allowing them to make informed investment decisions.
But the changes do not need to be big or cost a fortune. Sometimes it is the smallest considerations that can have the greatest impact on the performance. Indeed, at Besblock, ConSpare recommended a slight change to the position of the mixer which meant they could reduce the number of conveyor belts and allow two mixes to go into the hopper at once. This now gives the next batch longer in the mixer, improving the quality of each mix.
As mix designs become increasingly complex, it is important to analyze every application in detail to make sure the mixers perform. Although it was a relatively simple modification, it resulted in a fundamental shift in how the plant works and, as a result, the TEKA mixer is able to operate at peak performance.
The team also introduced other key pieces of world-class technology along the production process which allowed the investment Besblock had made in the new TEKA mixer to really pay off.
(Image: Besblock have been able to ramp up production to meet their growth plans without compromising on quality)
They installed a new Hydronix HydroControl HC06 digital water control system, which automatically manages and adjusts the moisture content in each concrete mix, optimizing the mix design for consistent results while also reducing waste and, of course, improving the quality. By pairing the Hydro-Control with the latest sensors, the plant can now maintain the concrete quality and achieve a precise final concrete moisture with an accuracy of ±0.1% (absolute moisture).
They also fitted CDX mixer dust-extraction equipment, which, unlike other filters, is an integral part of the production line. This conical shaped filter cleverly purges the dust from the air and puts it back into the mixer in real time. It does not need to be cleaned and will not need replacing as often as regular filters. This has not only improved the working environment in the factories as no dust now escapes when the raw materials are loaded into the mixer, but has also hugely reduced waste and downtime for cleaning.
Investing in new technology is a must for forward-thinking concrete businesses but the equipment alone will not futureproof the plant. Block making is a delicately balanced process made up of many interdependent stages. Through the adoption of a process-led approach to investing in new technology, businesses will truly be able to optimize their performance now and for the future.
TEKA pan, planetary, turbine & twinshaft mixers. High efficiency, low maintenance mixing.
Measure moisture in aggregates and control water in the mixer with Hydronix
Improve working conditions and aid regulatory compliance whilst reducing product waste