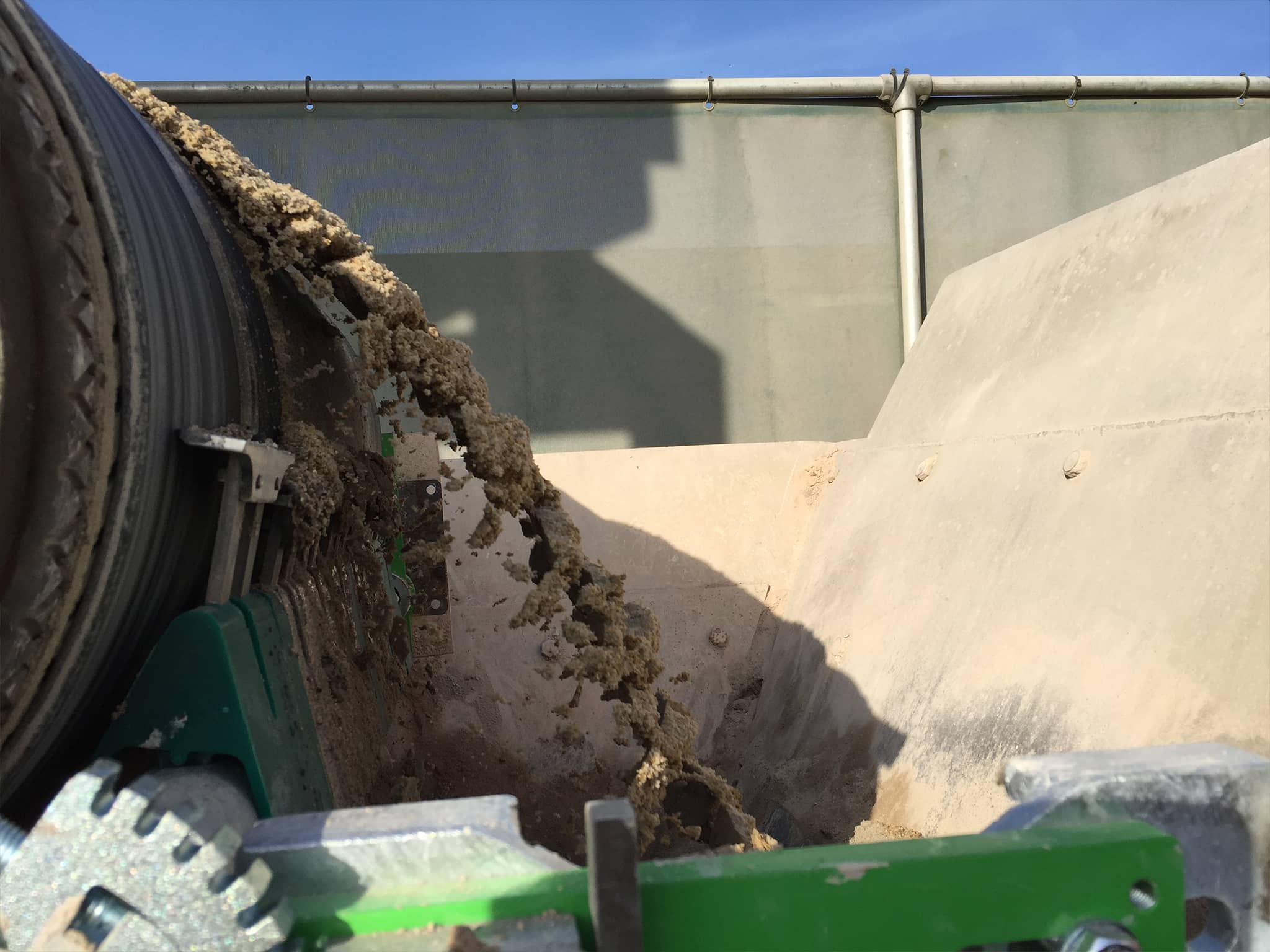
A leading building materials group with a large number of readymix plants has thousands of site staff across UK. The health, safety and wellbeing of team members is at the forefront of the business’s operations.
Belt cleaning is a long-standing and difficult problem within the concrete industry. Reducing carryback on belts helps prevent downtime, clean-up and reduces exposure to dust.
A readymix plant in the Midlands was struggling with clean-up of excessive carryback on a belt conveyor transporting sand and gravel around the plant. After three deliveries the tail drum of the drag-out conveyor was enveloped in roughly 0.5m of carryback. This resulted in an hour of cleaning and approximately 4 wheelbarrows of waste product removed each day.
(Image: Ineffective belt scraper covered in carryback)
Additionally, as the tail of the conveyor was below ground level in a pit, the staff often reported ailments associated with the manual labour required to clear the material. This was exacerbated in colder months and when the product got wet
The area general manager contacted ConSpare to see how we could help. One of our service engineers visited site to scope the conveyor. After listening to the challenges staff were facing, a primary position STARCLEAN® belt cleaner with 86n tungsten carbide blades was recommended.
STARCLEAN® primary cleaners are extremely effective at removing fines and moisture from the belt. The 86n abrasion resistant tungsten carbide blades ensure superior cleaning performance and minimal adjustment.
(Image: STARCLEAN® primary cleaner with tungsten carbide blades)
Previously, site staff were spending around an hour each day clearing carryback in the pit, removing around 4 wheelbarrows of wasted material. With STARCLEAN®, staff reported clearing out the area is no longer a concern, and clean-up now only takes around one hour per week.
Within the first 6 months of operation alone, STARCLEAN® has reduced cleaning time by an estimated 96 hours and eliminated 480 wheelbarrows of waste. Furthermore, the 75% reduction of time spent in the pit cleaning, and subsequent reduction in manual handling risks, has greatly improved staff welfare. The Plant Supervisor commented:
“This was a task that nobody wanted to do. It was demotivating, and the physical nature of shovelling the material was often demanding on the body and increased the risk of injury.
STARCLEAN® makes coming to work less stressful. Knowing I won’t have to get in a pit to shovel materials out each day means I can instead focus on value adding tasks.”
• Staff required to enter pit to clean-up carryback
• STARCLEAN® belt cleaner installed
• Clean-up time in pit reduced by 75%
• Staff welfare improved