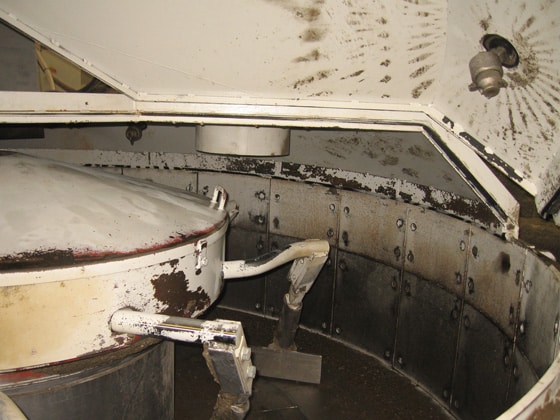
The operators at a busy readymix plant in the south of England, producing ~200m³ per day, were well-versed in living with the problems associated with concrete build-up on equipment.
The 2.25m³ twinshaft mixer was extremely difficult to keep clean. When originally installed, the mixer was specified with an OEM mixer washout system – but this proved ineffective and was removed by the site team many years ago.
Instead, a daily clean was performed via stoning out the mixer and hosing it down for 30 minutes. This approach had limited effect, so the team were required to enter the mixer for a manual clean once a week at the end of production – “gunning it out” for one hour with hand-held breaker tools.
This cleaning routine required operators to regularly work within a confined space and exposed them to HAVS risks. The task was also unproductive, and extended the team’s working day.
What’s more, as part of routine maintenance, the operators were required to clean down the mixer discharge chute on a monthly basis. The operation of dropping, cleaning, and repositioning the chute took over an hour to complete.
Already familiar with the success of WALTER cleaning systems within the client’s group, the Area Manager contacted ConSpare. A member of our Capital Division devised a custom solution which could both deep clean the twinshaft mixer, and also provide automated cleaning of the mixer discharge chute.
The mixer washout was spec’d with WALTER’s DAB pump unit and four RD3maX cleaning heads – generating an extra 25% power over the standard system, and designed to excel in twinshaft mixers. A fifth cleaning head was installed in the discharge chute, allowing automated cleaning at the end of each mixer cleaning cycle.
In the two years since installation, the results from the WALTER system can be summed up by the comments from the batcher:
“ The mixer is a hundred times cleaner now, it’s the best thing we’ve ever had installed on site.”
The daily use of the WALTER system and lance has resulted in the elimination of the weekly manual clean. Operators now only enter the mixer by choice, rather than necessity, to gun out any minor remnants for a short period once per month. This significantly reduces staff entry into the mixer, by around 45 hours per year.
The WALTER head in the discharge chute has eliminated the need for operators to perform a monthly manual clean, and also removed the troublesome task of dropping the chute and repositioning it after cleaning. The combination of the WALTER system and ConeFlex liner have made this a “fit and forget” area.
Overall, operators are exposed to less risk, undertake fewer laborious tasks and perform less ‘out of hours’ work – resulting in improved staff safety and better wellbeing.
• 2.25m³ twinshaft mixer suffering from concrete build-up
• Weekly manual clean undertaken by site staff
• WALTER installed in mixer and discharge chute
• Operator safety and wellbeing improved