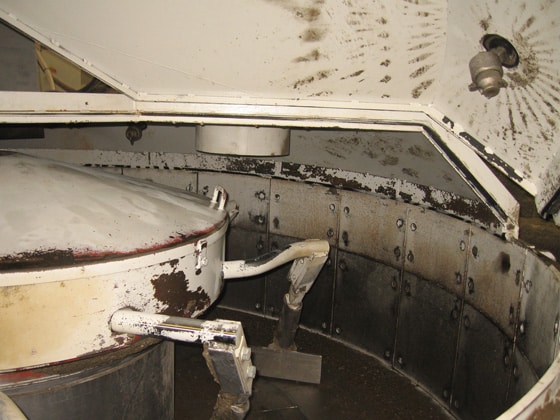
Keeping concrete mixers clean is a key factor in ensuring the batch plant stays productive. Often, the task of cleaning the mixer remains a manual operation and relies on the efforts of site operatives. This not only exposes staff to risk in a confined space, but also directly impacts their welfare and wellbeing.
Within a national readymix producer, a plant was having problems with concrete building up within their single shaft mixer. The build-up would routinely form on the mixing shaft, arms and blades. It would also build-up below the inlet’s sliding door, which would affect operation and restrict it from closing.
(Image: Concrete build-up in the single shaft mixer)
To combat the continual build-up, site staff would get into the mixer and clean it on a daily basis. 1-2 hours were spent undertaking the task with hand-held breaker tools, which exposed the team to HAV risks, dust and other ailments.
Additionally, when build-up became severe, a team of 2-3 maintenance staff would undertake a deep clean of the mixer. Typically, this would happen on a monthly basis and take a full day to complete, reducing the availability of the plant.
ConSpare has supplied hundreds of automated mixer washout systems in partnership with worldwide leader Walter Gerätebau GmbH. Having seen the success of a Walter system at a sister site, the operations manager asked us to help on their plant.
The ConSpare Capital Dept. visited site to assess the mixer. They specified a Walter DAB with two RD3maX cleaning heads. The double pump 120 bar unit outputs 100 litres of water per minute sequentially from each head, and the maX technology ensures even the furthest reaches of the mixer are cleaned effectively.
All installations are customised to best suit the mixer and client requirements. In this case, housings were fabricated to mount the RD3maX cleaning heads at a 30° angle and extensions were utilised, all of which ensured optimum cleaning angles and geometry were achieved. The client also requested installation of an additional hand lance at ground level for other cleaning tasks.
(Image: Single shaft mixer following automated cleaning cycle)
The results reported since installation of the Walter system have been impressive. The client runs an automated cleaning cycle twice a day alongside a wash down with the hand lance. Site staff haven’t had to enter the mixer for cleaning and the use of vibratory hand tools has been eliminated, significantly reducing risk and saving 1-2 hours per day in maintenance. The monthly deep clean has been eliminated, gaining an additional operational day each month. The inlet door is now completely un-obstructed.
Critically, the welfare of site staff has significantly improved. Ailments associated with entering and cleaning the mixer have reduced markedly, the team get to finish the shift on time, and morale has risen. The team are also able to spend more time tackling other issues on site and can contribute to making the plant more productive.
(Image: Head mounting customised to optimise cleaning pattern)
• Daily cleaning of mixer required with vibrating hand tools
• Monthly deep clean required, using 2-3 staff
• Walter washout system installed
• Staff no longer entering mixer for cleaning